Les objectifs du Lean management
1.1. C’est un système d’organisation du travail qui cherche à réduire tout ce qui fait obstacle à
l’efficacité d’une unité de production et à réduire, en particulier, les 3 types d’obstacles suivants
Les activités
sans valeur pour le client (« Muda »), notamment les 8 types suivants de
gaspillages : la surproduction, les attentes, les rebuts-retouches/corrections, les gammes et processus opératoires mal adaptés, les transports/ruptures de flux, les mouvements inutiles et les stocks (productifs ou administratifs), la non-utilisation des ressources intellectuelles du personnel.
Les processus
non adaptés (« Muri ») qui engendrent des
« surcharges déraisonnables » :
-pour le personnel, lorsque la charge de travail n’est pas adaptée au nombre de travailleurs ;
-pour les installations, lorsque la charge est supérieure à ce qu’une installation peut faire ;
-pour les coûts et les stocks, lorsque des pièces ou des produits ne « tournent pas ».
Les facteurs d’
irrégularité du débit de la chaîne de production
(« Mura »).
Les machines dont le temps et la qualité varient pour faire la même chose ; les opérateurs dont le travail varie pour la même production ; les fournisseurs dont les quantités et qualités de livraison varient pour la même commande.
1.2. C’est aussi et surtout un système de gestion de la
qualité et de management des hommes ; une méthode de résolution des problèmes visant à «
l’amélioration continue » (« kaizen ») par des actions concrètes, simples et peu onéreuses plutôt que par des innovations radicales, par des actions proposées et entreprises par les
acteurs concernés plutôt que par la direction.
Voici quelques présentations simples faites par M. Ballé, expert français du domaine :
(Sources :
https://www.youtube.com/watch?v=zWFcHc4daFw –
https://www.youtube.com/watch?v=OfswK6ebrt8 )
-Le «
Kaisen » a deux objectifs principaux :
-réduire les coûts en améliorant la qualité, les délais et la productivité;
-développer une culture d’entreprise donnant plus de sens et d’autonomie au travail.
-La
performance résulte de la capacité du management de former les personnes (développement individuel, travail en équipe, autonomie) et de mettre en place les processus qui appliquent le « Kaisen », comme l’indique le schéma ci-dessous :
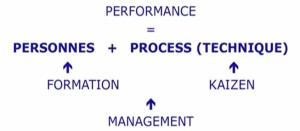
-Les
résultats de tous sont obtenus par la
contribution de chacun.
-La
motivation vient du succès et pas l’inverse.
-La fonction du
manager est de réduire ou supprimer les barrières à la réussite de ses collaborateurs.
-Les
changements d’attitudes indiqués dans le schéma suivant sont nécessaires : abandonner et au moins réduire nettement le recours à la pression comme moyen de faire acheter, résoudre les problèmes internes et rendre bénéfiques les relations avec les fournisseurs ; et adopter une attitude générale de coopération.
- Les principes de mise en œuvre
2.1. Le processus.
Inspiré de J.Womack et D. Jones dans « Lean Thinking », il est illustré par le schéma suivant :
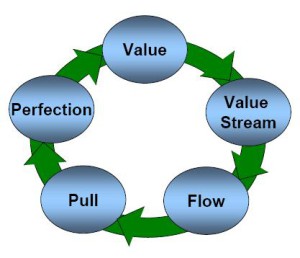
-Identifier les clients et déterminer strictement la
valeur attendue par eux (attentes explicites et implicites de qualité, délais, prix, etc.) et, donc l’offre à proposer.
-Définir la chaîne de valeur à réaliser et la
visualiser (« Value Stream Mapping ou VSM ») : définition des flux physiques et des temps d’écoulement, de l’entrée des matières premières à l’expédition des produits finis emballés : temps de chaque étape, délai entre 2 étapes, valeur ajoutée, indicateurs de performances à afficher, etc…)
-Veiller à l’écoulement continu du
flux des produits, services et informations de bout en bout.
-Passer du flux « poussé » par l’entreprise au
flux « tiré » par la demande du client : n’est lancé en fabrication, voire en approvisionnement, que ce qui est commandé par le client.
-Maintenir pérenne la dynamique d’
amélioration continue, processus de progrès permanent.
2.2.
Les outils utilisés.
Ils sont divers, les plus connus étant les suivants :
-La méthode des «
5.S » (5 premières lettres de mots japonais), illustrée par le schéma ci-dessous, a pour objectif de repérer et d’éliminer les causes de nombreux petits problèmes, sources de perte d’efficacité sur le poste de travail ou dans l’ensemble de la chaîne de production.
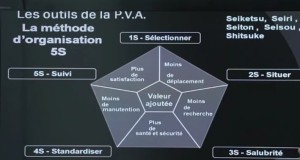
– La méthode des «
5 pourquoi ? ». Elle a pour objectif d’aller de la détection d’un problème à la découverte de sa cause fondamentale; par exemple, la question « pourquoi telle machine ne démarre pas » peut révéler la cause immédiate ; mais pourquoi cette cause est-elle intervenue ? Pourquoi, etc. ? On peut ainsi, pas à pas, approfondir la chaîne des causes et aboutir à un défaut de maintenance ou à un dysfonctionnement du système en place (non détection ou raisons d’apparition).
-La «
Value Stream Mapping ». C’est la visualisation des processus qui amènent un produit d’un état initial à un état final ; elle donne une représentation de la valeur ajoutée à chaque étape ; une représentation du temps de défilement du processus ; indique les objectifs et indicateurs de performance à réaliser. Cette visualisation des différents flux de matière, de travail, d’utilisation des équipements et d’information permet aux opérateurs de repérer les gaspillages et de proposer des actions correctrices. Chaque zone ou service doit « voir » la schématisation qui le concerne ; étudier les écarts significatifs par rapport aux objectifs fixés et monter un plan d’action correctif.
–
La Roue de Deming, symbole du cycle de l’amélioration. C’est une méthode de recherche de l’amélioration continue dite « PDCA » (W.E. Deming) illustrée par le schéma suivant :
http://www.kaizen-skills.ma/pdca-la-roue-de-deming/
P= « Plan » = Planifier le travail à effectuer et établir les objectifs.
D = « Do » = Réaliser les tâches prévues.
C= « Check » = Evaluer les résultats.
A = « Act » = Agir, analyser et corriger les écarts indésirables aux résultats.
La méthode consiste à réaliser tout travail en pratiquant successivement les 4 phases PDCA et en « faisant des tours de roue » tant qu’on n’a pas atteint l’objectif défini.
- Facteurs de rejet et conditions de l’adoption.
3.1. Les raison de rejet.
Les principes du Lean Management sont aujourd’hui mondialement connus mais peu appliqués complétement. En France, en fait, ce sont principalement les méthodes visant à la réduction des coûts qui ont été mises en œuvre suscitant de vigoureuses remises en cause.
-Une étude de la DARES (Ministère du travail) montre que les conditions de travail et la santé au travail sont
moins bonnes dans les organisations en Lean production que dans les organisations tayloriennes.
-Selon l’ANACT, plusieurs études et communications scientifiques alertent sur les
risques de dégradation des conditions de travail qui sont entraînés par le Lean management.
-Des auteurs expliquent que la suppression d’activités jugées comme des gaspillages par le Lean sont des activités à
forte « valeur ajoutée » pour les conditions de travail ; par exemple : les déplacements et changements de posture de l’opérateur contribuent à la prévention des troubles musculo-squelettiques ; les temps d’échange et les stocks intermédiaires entre postes facilitent la coopération entre les personnes.
-Des ergonomes, psychologues et spécialistes du travail alertent sur le fait que la recherche poussée du profit par la réduction des gaspillages peut aussi s’avérer
dangereuse pour la santé des travailleurs (stress excessif et troubles musculo-squelettiques).
-Le Cabinet Julhiet énumère comme suit les arguments principaux des anti-Lean Management
.
(
http://www.julhiet.com/2813/infographie-bruler-lean-management/).
Le Lean :
–
stresse les salariés ; il intensifie le travail et suppriment les temps-morts ;
–
manipule les salariés : l’amélioration de la productivité peut avoir des conséquences négatives sur le bien-être au travail et sur l’emploi ?
-a été
dévoyé en Europe : trop souvent, les décisions directoriales ont été préférées aux propositions de la base, la logique du court terme à celle du long terme, le changement de rupture au principe d’amélioration continue.
-est
trop exigeant en standardisation ce qui supprime des marges de manœuvre et tue la créativité.
3.2. Les conditions de l’adoption du Lean management
L’application des principes du Lean management impose de profonds changements dans les organisations actuelles encore largement tayloriennes ; en particulier, un changement de culture, qui demande du temps et de l’accompagnement.
3.2.1. Un pacte social pour recréer la confiance.
Ce peut être la première mesure de nature à surmonter les réactions de rejet. L’utilisation des
gains financiers de la méthode doit faire l’objet d’un accord qui définisse la part accordée
aux salariés et les formes de cette attribution.
3.2.2. Une décentralisation suffisante de la résolution des problèmes.
Les acteurs du « terrain » sont les mieux placés pour connaître les problèmes, proposer les voies de solution et mettre en œuvre les solutions retenues… si la direction donne la vision, l’orientation, les objectifs etc. et si les managers les plus proches d’eux donnent surtout l’aide nécessaire pour réduire ou supprimer les barrières à la réussite.
Ce nouveau type de
répartition des pouvoirs, étranger aux organisations tayloriennes, ne peut être mis en place que lentement et avec l’aide d’accompagnateurs.
3.3.3. Des managers particuliers et soutenus par leur direction.
(Source : M. Ballé, Lean Enterprise Télécom Paris,
http://leaninstituut.nl/publications/lean_attitude.pdf)
Pour comprendre et réussir la transformation Lean, il faut retenir que le Lean management est une
attitude face aux problèmes de gestion, une façon de penser, de se comporter, de réagir qui ne mobilise pas que nos facultés cognitives, celles qui nous font maîtriser intellectuellement les concepts et outils, par exemple.
-Le manager Lean est le plus souvent une sorte d’
obsédé du processus d’apprentissage et d’amélioration continu car, comme la plupart des innovateurs, il éprouve une irritation constante face aux opérations inutiles et un besoin acharné de « creuser » le problème pour y mettre fin.
-Il tend à penser que les dysfonctionnements ont des
causes systémiques et non individuelles et ne peuvent être traités que collectivement.
-Il préfère lancer rapidement, expérimenter, puis améliorer une
solution imparfaite plutôt que d’attendre la découverte de la solution parfaite.
On sait que les organisations encore tayloriennes d’aujourd’hui ont du mal à soutenir de tels managers.
Eux seuls, cependant, à condition d’être en nombre suffisant et soutenus par leur direction, sont capables de servir de modèle et de produire dans les entreprises les effets bénéfiques du Lean management.
Aucune reproduction, ne peut être faite de cet article sans l’autorisation expresse de l’auteur ». A. Uzan. 29/02/2016
>